- Scientists always knew lithium metal could revolutionize batteries, but they have one fatal flaw: they often short circuit.
- No one knew why this happened—until now.
- Now, scientists can build better lithium-metal batteries to eventually produce more electric vehicles.
Also Read– Why Apple, Amazon, and Meta Platforms All Fell on Microsoft’s
When looking for an anode material for your next-gen battery, you can’t do much better than lithium metal. Due to its high capacity, low density, and non-flammability, lithium-metal batteries could be an absolute game changer for electric vehicles and the green tech revolution at large.
There’s just one problem: Lithium-metal batteries have a tendency to short circuit thanks to tiny fissures in the ceramic electrolyte called dendrites.
The quest to figure out why this happens (and design a battery that circumvents this unfavorable outcome) is a Holy Grail of sorts for material scientists—and the science world has maybe found its Galahad.
This week, researchers from Stanford University and the SLAC National Accelerator Laboratory revealed evidence as to why these dendrites form within lithium-metal batteries.
Also Read- How to Prevent a Flu Outbreak at Your Business
Previous theories have suggested unintended electron flow or some other mishap of chemistry could be the cause of the battery’s failure. But after conducting more than 60 experiments, the researchers discovered that small “nanoscopic” cracks in the ceramic solid electrolyte, some as wide as only 20 nanometers (a human hair is 80,000 nanometers by the way), occur when under pressure during fast charging.
These cracks allowed a lithium-metal “bridge” to form between the anode and cathode, causing a short circuit. The results were published in the journal Nature Energy.
“Just modest indentation, bending or twisting of the batteries can cause nanoscopic fissures in the materials to open and lithium to intrude into the solid electrolyte causing it to short circuit,” lead coauthor William Chueh says in a statement. “Even dust or other impurities introduced in manufacturing can generate enough stress to cause failure.”
The researchers combined an electric probe and an electrolyte to create a miniature battery in an attempt to understand why lithium burrowed into certain areas and caused a short circuit. When resting, the lithium anode performed as designed, but any indenting, bending, or twisting (along with specks of dust gathered during the manufacturing process) increased the chances of failure.
Also Read– Trellus Local Delivery Grants Available in New York
Lead coauthor Xin Xu compared the process to potholes. As car tires pound rain and snow into tiny imperfections in the road causing an ever-increasing structural failure, the same happens inside lithium-metal batteries (albeit on a much smaller scale).
Luckily, this isn’t a death knell for lithium metal’s future—in fact, it’s great news.
Now, engineers who are already hard at work designing lithium-metal batteries can take these findings into consideration to circumvent these shortcomings. The paper’s authors also mention that they’re now investigating ways to strengthen the electrolyte during manufacturing as well as develop ways to coat the ceramic barrier so that it self-repairs damage when it occurs.
In 2019, the same Stanford lab developed a method for lithium-metal batteries to retain 85 percent charge after 160 cycles—a major improvement compared to the previously reported 30 percent.
“These improvements all start with a single question: Why?” says coauthor Teng Cui. “Once we know that, we can improve things.”
Also Read– What to know before using a business credit card for your small business
Now that researchers have convincingly answered the question of why, the overall question of lithium metal’s future is looking less like “if” and more like “when.”
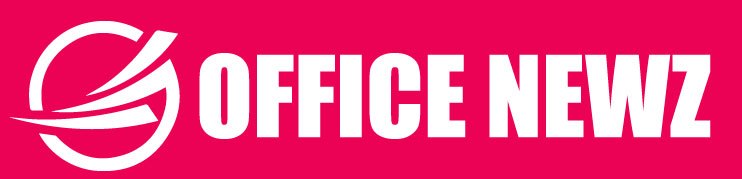